Based in Southwark, Fuse Architects are a proudly People First practice and they project that core value into everything they do, from their employees to the people they work with and deliver for. Fuse Architects have a strong commitment to social value and social responsibility, believing in innovative, responsible design with commitment to balancing customer satisfaction with a sustainable approach to architecture. They have been at the forefront of designing and delivering net zero carbon, affordable housing and are a 2030 Climate Challenge Signatory .
Fuse Architects provide a full range of design and technical services, working on all RIBA stages (0-7) with specialist expertise in residential developments, affordable housing and community developments.
In 2019 they were Southwark Business Excellence as Employer of the Year, and are proud to have won the Offsite Social Housing Project award in September 2021! They've also been shortlisted in the 2021 London Construction Awards and Constructing Excellence Awards and shortlisted for Building Awards 2021.
RIBA London asked them a few questions about sustainability how to sell it to clients and how they use Offsite Construction Manufacture to meet their zero carbon goals.
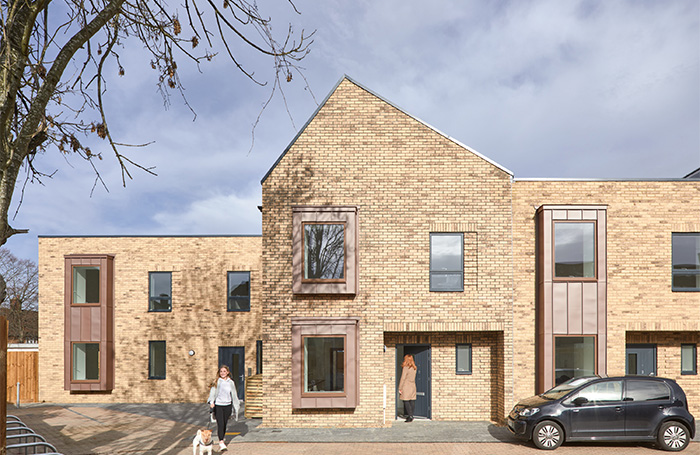
What’s the most exciting project you’ve got coming up and why?
The Underwood in Greenwich is part of the Greenwich portfolio and was awarded Offsite Social Housing project of the year. It has delivered 8 affordable homes and 1 wheelchair home at net zero carbon, with fuel bills at £200 pa. With current news highlighting rising fuel bills we are proud to have designed and delivered this scheme as well as another eight schemes, which will be delivering this design.
A lot of your projects use Offsite Construction Manufacture. How can MMC and OSM contribute to a reduction in environmental impact?
Offsite Manufacture and Modern methods of Construction have an important role to play in the reduction of environmental impact such as reducing carbon, both embodied and operational. OSM enables a far greater reduction in waste than traditional construction on site. Factory conditions, manufacturing processes and quality control significantly improve the efficiency of material usage and reduction in waste. Waste can also easily be collected and recycled within the factory. OSM, and controlled factory environments, also enables greater air tightness within the building fabric reducing air leakage and improving thermal performance. This in turn reduces the amount of energy needed to heat the buildings (be lean). MMC can also help with enhanced insulation and therefore thermal performance by reducing gaps, misaligned insulation and fitting issues to almost zero. This creates a better insulated envelope reducing energy use (be lean).
You're a signatory to the RIBA 2030 Climate Challenge. How are clients reacting to your Sustainability and Zero Carbon commitments?
Clients are all looking at including net zero carbon solutions in their development program, this is ever more necessary with changing legislation and the emerging climate emergency, we have approached this simply and provide an informal free Net Zero Carbon webinar on our approach and design, this has been well received by clients and end users.
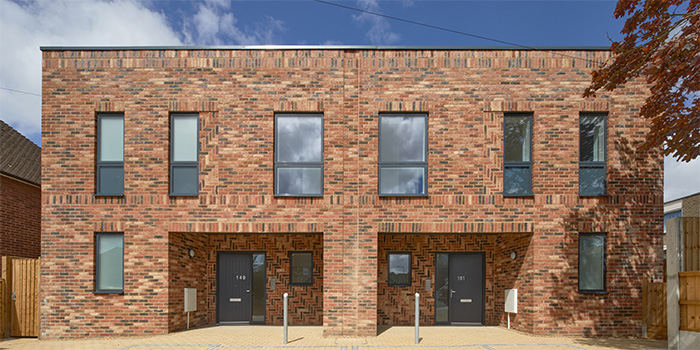
How does the end user benefit from low carbon homes?
Simply put they benefit from fuel bills under £200 per annum, it eradicates fuel poverty which is a huge benefit!
Do you see a direct link between zero carbon projects and health and wellbeing?
Absolutely. After 18 months of lockdown and the issues faced by many households addressing fuel poverty is a huge benefit to the health and well-being of households. We have also worked with end users on training and info packs on how to use the technology and we have seen enormous benefits as families embrace this technology.
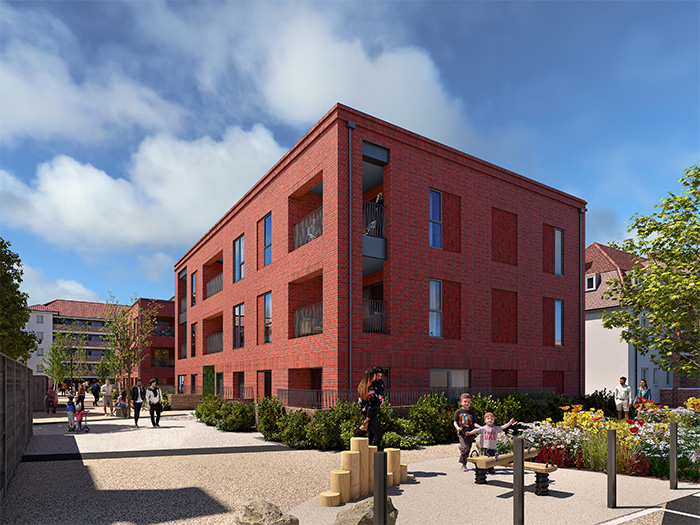
To find out more about Fuse Architects, visit their website or follow them on Twitter, and LinkedIn.