Government supports the expansion of heat networks
At the turn of the year, the UK government announced a major expansion of heat networks in the country, with a £19 million contribution to the setting up of five new networks in Bristol, Liverpool, London, and Worthing. Funding comes from the Heat Networks Investment Project (a fund of £320M) launched in 2018, as well as a second capital grant fund, the Green Heat Networks Fund totaling £288M.
The government views heat networks as one of the most cost effective routes long term to decarbonise the country’s heat supply, according to Simon Woodward, Chairman of the UK District Energy Association.
While the majority of existing networks are still supplied by gas, the target is to decarbonise them by the early 2030s. Any new ones being built now should draw from low carbon heat sources such as recovered heat from the likes of waste plants, data centres, sewage works, industrial facilities, and even large rivers.
Zoning and local planning requirements expected to drive heat network readiness in urban areas
Dubbed ‘central heating for cities,’ heat networks currently meet roughly 2% of UK heat demand, but the government targets around 20% by 2050.
To aid their growth, the recent Energy Security Bill (ESB) is set to introduce heat network zoning into UK urban areas, mandating the connection of many types of buildings to heat networks. It is expected to pass into Royal Ascent during the first half of 2023 and to come into force by 2025.
As a result of zoning, new builds and existing housing stock, that either have existing communal boilers or are being refurbished, will be required to connect to heat networks where they are being developed or exist already.
In addition to national regulation of heat networks including their design, local authorities in London can now require designers to include heat loss calculations for heat networks on developments as part of the energy assessments for planning applications. They must also demonstrate that all steps have been taken to reduce these losses as set out in the GLA Energy Assessment Guidance published earlier in the summer.
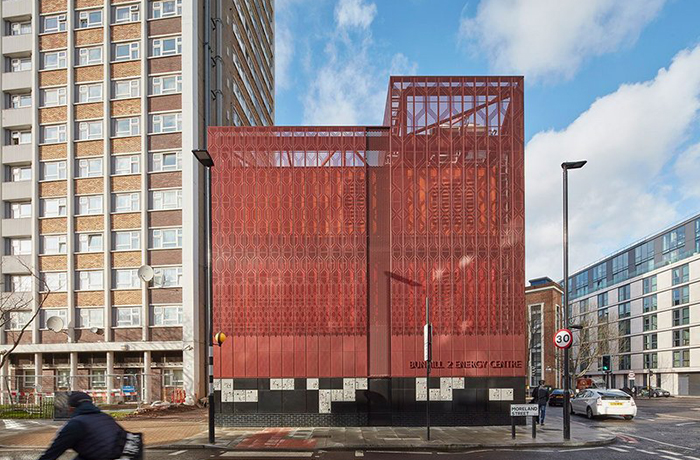
Building design makes or breaks the efficiency of heat networks
However, concerns have been expressed that architects and developers are not adequately aware of best practices for their implementation and the huge impact that very early stage design decisions, such as building layouts, can have on heat losses in operation.
This view is shared by Simon Woodward, who explains:
"The Chartered Institution of Building Services Engineers Code of Practice: Heat Networks is a voluntary code of practice for the design, development, and operation of heat networks. It clearly sets out how to design buildings to reduce heat losses.
However, because of its mechanical-electrical focus, few architects will have heard of it, let alone read it in detail. Running to hundreds of pages, it's a lot to wade through even for people in the sector.”
This lack of familiarity with the technology means there is a widespread failure for heat networks to be planned into projects early enough or optimally. As a result, Woodward says, some new build housing developments are seeing less than half of the heat produced actually making it to dwellings.
This can exacerbate the current energy cost squeeze experienced by households and makes it all the more important to optimise building designs for heat network efficiency.
Pipework length is a crucial factor in minimising heat loss
“The main problem is that the mechanical layout of pipework within blocks of flats is thought of as almost the final piece of the jigsaw puzzle. This commonly leads to very long runs of pipework and hence, by the time the problem is recognised, unavoidable levels of heat losses. The design team does not typically think about the impact of the decisions that they're making on the mechanical pipework at the time when they should.”
Ideally, the length of internal heat networks should be a total of no more than 10 metres for flow and return per dwelling across the entire building. Woodward, who also works as an independent consultant, is seeing developments being built where the figure is over 25 metres - a 60% overshoot. The primary reason for this, he says, is a lack of risers being planned into buildings.
"My perception is that architects and building developers don't like building in vertical pieces of architectural structure that can carry mechanical pipework up through the building. That's because they may encroach on lettable or sellable area - and so typically, we find that the number of risers will be limited.
Quite often I've worked on developments where there's only one riser for a whole block of flats. That means you have very long runs of pipework called 'laterals' running down the corridors to connect individual dwellings, adding up to excessive total lengths of pipework."
This problem can be exacerbated in dwellings themselves, which might see pipework routed around their perimeters before they connect into the dwellings’ heating/hot water systems to accommodate other design choices, thereby further extending the flow and return distance.
Building designs need to accommodate appropriate insulation levels
Another major issue is a failure to use pipework with the requisite insulation - or a failure to plan in the space required for that size of insulation.
To achieve the low level of heat loss required, 75 millimetres of insulation is often needed – significantly more than the 25 millimetres that Woodward says is typically designed in by default.
“Commonly, architects are not thinking about how big a riser cupboard needs to be or how big a space in the ceiling needs to be to accommodate pipes with this level of insulation thickness,” he explains.
Insufficient pipework insulation can cause overheating
A side effect of this, in addition to a loss of efficiency in heating dwellings, can be buildings overheating in other areas, such as corridors along which laterals are running.
Woodward cites some worst cases in which air conditioning units have been installed in corridors to reduce the temperature caused by the loss of heat through overly long runs of pipework that is inadequately insulated – a dizzying proliferation of inefficiency.
Total pipework length within a development, and insufficient levels of insulation, are the two biggest causes of high heat loss. Related to the latter, inadequate insulation on valves, fittings, and pipe support is another.
Among others are heat interface units with high standby flow rates, higher than necessary flow temperatures, and oversized pipes, with heat loss reduced by 10% for each size down.
Architects have a big role to play in enabling optimal efficiency
“Architects have a big role to play in enabling the optimal efficiency of heat networks,” Woodward confirms.
The CIBSE Code of Practice provides simple diagrams to help designers and clients apply these principles in their designs. A pertinent example can be found in "Objective 3.9: To achieve an efficient heat distribution system within a multi-residential building, and to reduce the risk of overheating".
Importantly, Woodward recommends architects involve mechanical engineers from the early design stages to minimise these losses and build in compatibility with a technology set to contribute a substantial share of the country’s heat supply in the near future, thereby reducing carbon emissions and exposure to fuel poverty.
Thanks to Simon Woodward, Chairman, The UK District Energy Association.
Text by Stu Roberts. This is a Professional Feature edited by the RIBA Practice team. Send us your feedback and ideas.
RIBA Core Curriculum topic: Legal, regulatory and statutory compliance.
As part of the flexible RIBA CPD programme, professional features count as microlearning. See further information on the updated RIBA CPD core curriculum and on fulfilling your CPD requirements as a RIBA Chartered Member.